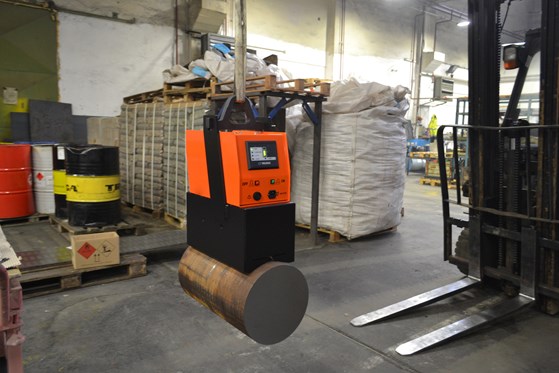
A battery-powered lifting magnet with remote control.
Pay close attention to the type of the lifting magnet and its lifting capacity. Take into account general conditions in your warehouse or production plant. Inquire about the magnet’s quality and certification. Read on to learn more tips on choosing the optimal lifting magnet.
Types of Lifting Magnets
Each type of lifting magnet comes with its set of pros and cons:
- Permanent lifting magnets: The magnetic force is switched on and off by a manual lever. Permanent lifting magnets are made of neodymium, iron, and boron, and their key characteristic is that they don’t need to be plugged in. This translates to independent, electricity-free functioning — but also to limited lifting capacity (approx. 2 tons) as it would be impossible to switch the ON/OFF lever by hand on more powerful permanent lifting magnets.
- Battery-powered lifting magnets: Activated and deactivated by a switch button — no manual force is required when switching a battery-powered magnet on and off. This means that such a magnet can be more powerful (with higher lifting capacity) than a permanent one. Another benefit is that the lifted load gets automatically demagnetised once the magnet is turned off. The cons of battery-powered lifting magnets are their higher price and the fact that their battery needs to be charged.
- Lifting electromagnets: Also turned on and off by a switch button, but instead of being powered by a battery, connection to a power source is required. Thanks to that, the lifting capacity can be very high — 5 tons and more.
- Electropermanent lifting magnets: Halfway between permanent magnets and electromagnets, an electropermanent magnet is activated by an electric impulse — it needs to be plugged in only at the time of activation. Once activated, the magnet doesn’t need electricity any more. The pros of electropermanent lifting magnets are their high lifting capacity and the fact that no electric cable gets in the way when working with the magnet. Higher residual magnetism is the con — workpieces need to be demagnetised after the magnet is deactivated.
OUR TIP: We recommend reading our comprehensive guide to magnets if you want to learn more about various types of magnets: Differences between permanent and electropermanent magnets and electromagnets. |
Maximum Lifting Capacity
Lifting capacity is the first parameter you should inquire about when choosing a lifting magnet — it should always be clearly stated on the magnet. The EN 13155:2020(E) standard for lifting magnets sets the following requirements for lifting capacity:
- Permanent lifting magnets are required to safely lift loads 3× heavier than their maximum lifting capacity.
- Battery-powered lifting magnets should safely lift a load 2× as heavy as their maximum lifting capacity.
- Electropermanent lifting magnets should be able to lift and hold loads 3× as heavy, with instant monitoring of their holding force (which should be 2× their nominal lifting capacity).
This might look like there’s such a reserve that respecting the nominal lifting capacity is not so important. That’s not the case. Never exceed a lifting magnet’s maximum lifting capacity!
Bear in mind that magnets’ nominal lifting capacity is measured in ideal conditions which rarely occur in reality. In practice, load gets dirty, dusty, it might be covered with residue paint, or it could be rusty — all of which decrease a lifting magnet’s holding force. When lifting thin metal sheets, for example, air gaps form between the sheets, making the magnetic force less effective.
The holding force of a neodymium lifting magnet (and consequently, its lifting capacity) gets negatively affected by higher temperatures (over 50 °C). For hotter conditions, pick lifting magnets made of samarium and cobalt — such as our NEO HOT lifting magnet line.
OUR TIP: Read this article to learn more about the lifting magnets’ certification. |
Here's a demonstration of how friction force affects the overall holding force
of a lifting magnet.
Lifted Load
The material and shape of the lifted load matters. To get the optimal lifting magnet, consider these parameters:
- Load Material. Low-carbon steel (C15 nebo C22) streams the magnetic flux the best. High-carbon and alloy steel are less ideal.
- Load Shape and Proportions. Very long metal sheets tend to bend and/or slide down when lifted. Large magnetic systems prevent that from happening.
- Load Thickness. When it comes to thin metal sheets, the magnetic field permeates through them and closes behind them — weakening the magnetic force. The same happens when handling metal sheet bundles — air gaps between the sheets are at fault here.
How to Spot a High-Quality Lifting Magnet
Cheap, low-quality lifting magnets are unfortunately common on the market — avoid them. Your first red flag should be a price that is too low to be true. Careful here! Cheap lifting magnets often come from China or elsewhere in Asia and don’t comply with European safety standards. To spot a high-quality magnet, pay attention to:
- The construction of the magnet. High-quality lifting magnets are welded from one piece of metal, with no bolts in the construction whatsoever. Lower-quality magnets are just bolted.
- The switch lever. It should always be possible to switch the lever by hand, and the lever should never shoot back to the OFF position on its own.
- A high-quality lifting magnet is always compliant with the EN 13155:2020(E) safety standard. We recommend requiring compliance also with the European CE standard.
OUR TIP: We went into detail about magnets’ quality in our article How to spot a low-quality magnet. |
Get Advice from the Manufacturer
High-quality lifting magnets last for decades when maintained well. In case you need advice, do not hesitate to consult your manufacturer or supplier.
At Walmag, we always consider the specifics of your facilities and lifted load when helping clients pick the best lifting magnet. We even lend lifting magnets to those considering them — to try them out and decide later. We design and manufacture large lifting systems or customised lifting magnets for larger facilities.
OUR TIP: Get inspired and read our case study on how lifting magnets make production more effective at SIEMENS. |