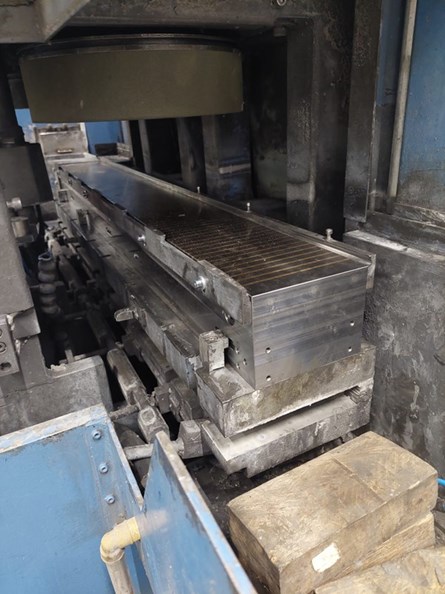
Quick response, proactive approach, error-free and on-time delivery — that's how Jan Šettner, the technologist of SCHOTT, describes working with Walmag. We made a new magnetic chuck for the grinding machine they were using and even improved the original solution with a double switching mechanism. Two switching levers on both sides of the long magnet made the grinder operator’s job easier than before.
SCHOTT is a renowned global supplier of automotive parts. In its production facility in Lanškroun, Czechia, they produce heads for airbag igniters. These are crucial for airbag activation — thanks to them, the airbag inflates at the moment of impact. SCHOTT's customers are other suppliers within the automotive segment - e.g. .....
Heads for airbag igniters are made from small metal parts that need to be ground flat. It would be very inefficient to grind the heads one by one. At SCHOTT, they machine-grind the heads by batches of 50 or 60 pieces (the number varies depending on the igniter type). The grinder operator stacks the required number of heads in a grid which functions as a tray and a holder at the same time. The grid is then placed on a production conveyor belt on which the tray moves towards the grinder. Which grinds all headers in the tray.
Customised Magnetic Chuck for Sklopan Grinder
The tray with igniter heads is held firmly on the conveyor belt by a magnetic chuck placed under the belt. It’s of an unusually long shape and is supplied as part of the grinding machine used at SCHOTT. It’s made in Czechia (Sklopan from Liberec) but the magnet under the belt was supplied by a German manufacturer.
Jan Šettner, mechanical engineering technologist at SCHOTT, contacted us when he recognised that it was time to replace the magnetic chuck in their grinder. The magnetic plate of the magnet was already badly worn. That is normally solved by regrinding — but repeated grinding makes the plate thinner. At SCHOTT, the magnetic plate was already too thin to be ground again.
Apart from that, at SCHOTT they had long been unsatisfied with the original magnetic chuck because it couldn’t be switched off (it was a permanent magnetic technology with no switch lever). So when they needed to remove the metal bar that they put on the conveyor belt between the grid and the magnet, they had to get an entire team to do it. One operator wouldn’t be able to move the bar.
Jan Šettner approached the magnet’s original manufacturer from Germany at first. Without success. A Czech representative of the company was nowhere to be found.
''I didn't have the time and patience to wait for someone to reply. So I looked up other magnet manufacturers. I wanted to find a manufacturer, not a reseller, because I expected a professional approach and also available service if needed. Walmag seemed like a good fit — being also from Czechia, I thought that dealing with them would be easier and faster. I was right. Walmag's sales rep Petr Hulan replied immediately and in just a few days, he was already here for a meeting in person,'' praises Walmag's proactive approach Jan Šettner.
Petr Hulan from Walmag confirms his words: ''SCHOTT knew exactly what they wanted, so all they had to do was check that we could produce it and how long would it take us. Mr Šettner gave me a blueprint of the machine and with our engineers, I came back to him with a price quote. I almost hesitate to take credit for this job, I just responded when our German competitors didn’t.''
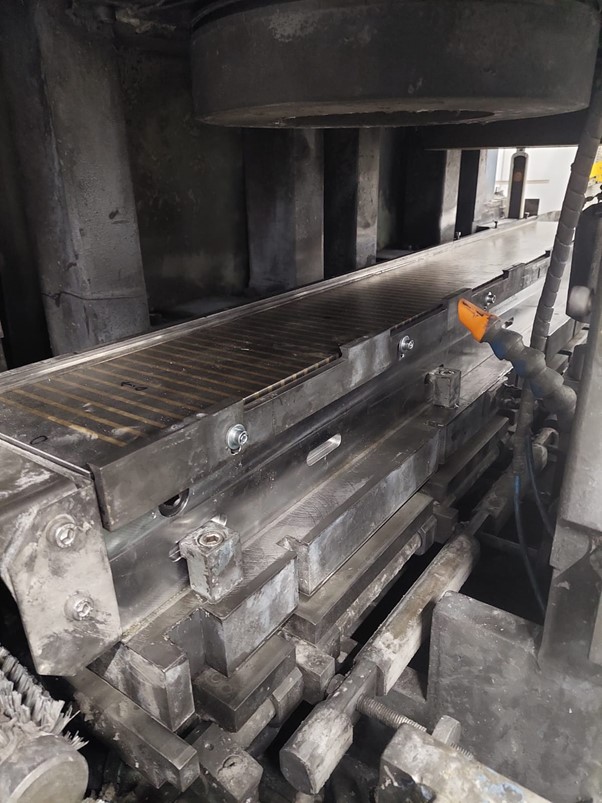
Magnetic Chuck for Machine Grinder: Technical Parameters
The grinding machine at SCHOTT contained a long permanent magnet. Their machining technologist wanted to keep the magnetic technology. Simplicity and affordability — both in terms of magnet price and power consumption — were his priorities. He didn't want to change the established production processes or have to figure out where to plug in the electromagnet or connect it to the grinding machine control unit. In addition, the precision machining they do at SCHOTT could get complicated by an electromagnet. It heats up when switched on, causing the workpiece to expand and reducing grinding accuracy as a consequence.
''For SCHOTT, we produced a permanent magnetic chuck based on our Neomill, and customised it. Its dimensions are quite unusual — 150 cm wide and 1,470 cm long. Guys in production nicknamed it dachshund,'' smiles Petr Hulan, Walmag sales representative.
To make it easy for the operator to work with such a long magnet, there are two switch levers on the grinder, each activating one half of the magnet. “With permanent magnets, you have to physically turn the magnetic core inside and that requires a lot of strength. One switch lever for such a long magnet would be really hard to switch. SCHOTT would need a muscle man to do it,'' explains Petr Hulan.
How to Regulate Magnetic Force of a Permanent Magnetic Chuck
The need to increase and decrease the magnetic force is usually the reason why companies get electro-permanent or electromagnetic magnetic chucks. SCHOTT wanted neither — besides their higher price, it would have meant modifying their production processes. They manage to adjust the magnetic force otherwise.
''We regulate the power of the magnet by inserting a millimetre-long planchet between the magnet and the production belt. This reduces the power of the magnet as part of the magnetic force is absorbed by the planchet. The workpiece holder is then held on the belt with less force. We do this because we need the tray to slide nicely on the belt so that the clamping magnet wears off less," explains Jan Šettner from SCHOTT.
A Less Expensive Alternative of the Magnetic Chuck
Walmag’s sales rep even offered SCHOTT a less pricey version of the magnetic chuck — we would have reduced the price by using epoxy as insulation instead of brass. SCHOTT did not ultimately choose this solution, but they liked the proactive approach to the order.
''Overall, I would rate the business with Walmag like this: professionalism, immediate response, helpfulness. We have other grinding machines with similar magnets in operation here and I'm positive that when the time comes to replace them, I will reach out to Walmag again. I have no doubt that their magnet will prove its worth over time. I just can't say that now with 100% certainty, we haven't been using it that long," assesses Jan Šettner from SCHOTT about his customer experience.‚
Delivery & Installation of the New Magnetic Chuck
Jan Šettner wanted to have the new magnet ready in advance so that he could act immediately when they’re able to stop the manufacturing processes at SCHOTT and have the magnet replaced.
The production of the customised magnetic chuck for SCHOTT took about 6 weeks. We delivered the magnet to SCHOTT in January 2024.
TIP: We have described the production of customised lifting magnets and magnetic chucks in one of our articles. |
We’re here for you! Happy to answer your questions — whether you need to replace a magnet in a machine or are just thinking about introducing magnets into your operations. You will find the contacts here.