
Zbyněk Tihelka, CEO
A switch lever that can accidentally turn the lifting magnet off. Thousands of euros wasted on a DIY magnetic lifting system. Or, in the worst scenario, a workplace injury. All that can be caused by low-quality lifting magnets and magnetic chucks. Zbyněk Tihelka, Managing Director of Walmag, has seen a lot over the past 23 years in the business. Here’s his take on the perks of cheap magnetic technology.
How to spot a “suspiciously cheap” lifting magnet or a magnetic chuck?
A quick market research before you buy is always a good idea. This way, you'll get a good grasp of the price range. Magnets that come at a suspiciously low price are usually of poor quality which translates to poor functionality and short longevity. But that’s not the only issue — you might encounter problems during shipping, and warranty and customer care might be non-existent. I recommend being wary with magnets with a considerably low price. I know a company that sells inexpensive magnets made in China as if they were made here in Czechia. But their super low price gives them away.
What is the most expensive component of a magnet?
That depends. The final price reflects high-quality materials, precise manufacturing, and the manufacturer’s know-how and used technologies which shape the magnet’s qualities. Premium magnetic materials are sometimes difficult to acquire. Take neodymium for example — it’s made mainly in China, so its price can be affected even by China’s changing policy. Not to mention the fact that Europe has a lot of rules manufacturers have to respect — with regard to environment, working conditions, certifications and more. That increases the final price as well.
Neodymium is used in permanent magnets. Does it mean electromagnets are cheaper?
Not really. Electromagnets don’t contain neodymium but you need copper or aluminium to manufacture the inner coils. Also, spooling the coils is quite time-consuming and requires great expertise. That increases costs as well.
Is there a cheaper alternative to neodymium?
You’ve likely come across ceramic magnets — it’s the kind people use to stick photos and notes on our fridges. They’re usually too weak to be used in a production facility. So there’s really no usable alternative to neodymium for manufacturing and warehousing purposes.
But the quality of neodymium may differ. Less expensive neodymium is weaker — to be exact, its volume contains less magnetic energy than neodymium of better quality. Or, there might be a higher percentage of faulty pieces in one batch.
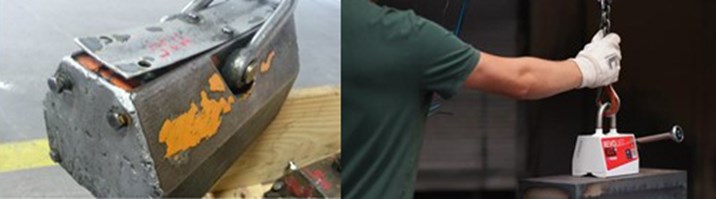
Left: A lifting magnet with a bolted construction that has already started to fall apart.
Right: REVOLIFT, the newest addition to Walmag’s lifting magnets portfolio. All welded, with only 2 bolts.
What about a magnet’s outer construction? Can we say the higher the price, the better the quality?
Undoubtedly. Higher price suggests that the magnet was manufactured with great care. And that its construction was developed with a deep understanding of the technology. Lifting magnets are a good example. At Walmag, we weld individual parts to make the construction of a lifting magnet. It’s definitely more expensive than if we’d just used bolts but it’s worth it — it makes our magnets strong and long-lasting.
Are welded magnets better than bolted?
A welded construction is robust, durable, and resilient. Most bolts get loose over time. And when that happens, the magnet starts falling apart, literally. A workplace security risk for sure! A welded construction doesn’t fall apart. But of course, using bolts to put a magnet together requires no machining expertise so it can be done for cheaper by less qualified staff. Operators who make Walmag magnets are true professionals and their work is precise. Great care is put on preparing the construction parts — the quality is in the detail.
Usually, only people with expertise from the machining industry are able to recognise a good-quality construction of a lifting magnet or a magnetic chuck. The obvious giveaway for people who aren’t experts is that all sides of the construction are perfectly flat and even, there are no sharp edges. Such a magnet lasts for years.
What about the quality of the switch lever?
Switch lever is another giveaway of a magnet’s poor quality. It should be precise and robust. It should have a safety switch so that the magnet can’t be turned off by accident. A while ago, I shared a video on my LinkedIn featuring an inexpensive lifting magnet without a safety switch. To make things even worse, the button that de/activated the switch lever was placed on its end. Extremely dangerous. Any time the magnet accidentally touched objects in its vicinity, it got deactivated by chance. I suppose I don’t need to describe what that could cause. It was a serious safety risk for any production facility or a warehouse.
What else is reflected in the price of lifting magnets and magnetic chucks?
I’ve already mentioned the expertise, especially with regard to inner parts of the magnet. Those have to be assembled by seasoned technicians, not by unqualified workers who are paid very little money. Tags on the magnet are also important, especially on lifting magnets. I once saw a lifting magnet with paper tags! That’s also a serious safety hazard — even metal tags get scratched and otherwise damaged when the magnet is used, let alone paper. A few weeks in operation and you won’t know whether the magnet is fit to lift 300 or 800 kilos.
A lifting magnet’s tag should always be easy to read and when it gets damaged, the magnet should be serviced or refurbished — according to European standards. Which is another issue with cheap magnets from Asia. Very often, they conform just to the bare minimum and at the slightest wear and tear, they easily fall under the set European standards.
At Walmag, we have a strict testing protocol for our certified lifting magnets — we guarantee that they should always be capable of lifting objects that weigh three times more than the magnet’s nominal lifting capacity, even with an air gap of 0.1 mm (a so-called AIR GAP TEST). High-quality magnets always come with proper documentation, testing protocols, and a user manual. If shipped, their packaging would be neat so that the magnets don’t get damaged during transport.
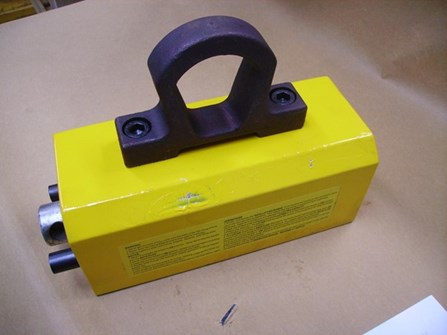
A lIfting magnet made in China. Its paper tag which will most
likely become illegible in just a few weeks.
Does lower quality affect the magnet’s functioning?
Safety risks are always heightened when clamped or lifted workpieces are not held with sufficient magnetic force. In addition, lower quality magnets often have higher magnetic residue which makes workpieces hard to remove, even after the magnet is switched off. That can get people in some potentially dangerous situations.
Low-quality magnets cause accidents from time to time. I’ve heard about such cases; once, I was approached by the police as they wanted my expert opinion on a workplace accident which involved a magnetic chuck. That’s a shame, because clamping and lifting magnets are in fact very safe to use, usually safer than manual clamping and lifting with ropes.
You mentioned safety certificates and rules. Are they reflected in the price as well?
Sure! At Walmag, we double-check everything, in all stages of our production. We have high standards and requirements when it comes to our suppliers and employees — the goal is to ensure the best possible quality of our magnets. Every magnet is thoroughly tested and controlled. We issue an individual certificate for each of our lifting magnets which claims their test results and nominal lifting capacity. As far as I know, only a few manufacturers do that.
Are there other downsides of using cheap magnets?
Well, you won’t be very happy when your magnetic solution doesn’t work, will you? Or when it works at first but then gets worn and torn so quickly that it stops being usable. I understand the temptation of saving a few hundred euros. But when the magnet you purchased fails you just as you’re finishing a job which could earn you thousands of euros, you may actually lose money. Are savings worth it when a lifted object falls down and gets damaged, or damages expensive production equipment? Let alone when it injures someone.
Another minus can be bad or non-existent customer care. What to do when a magnet malfunctions and no one comes to fix it? That’s when people sometimes approach us at Walmag and ask for help.
And do you help them?
Yes, if we can. But sometimes there’s nothing we can do. I remember a customer who tried to set up their own magnetic lifting system — they put 10 lifting magnets (each with a 500 kg lifting capacity) on a pole and intended to lift 12 metres long metal sheets with it. Each sheet weighed about 4 tons. If we were asked to put together a functional magnetic lifting system for these purposes, it would cost approximately 60,000 EUR. The customer thought they could make a DIY solution for about 4,000, without expert advice and proper calculations of the magnetic force (and other forces which affect the magnet). Unsurprisingly, the makeshift lifting system didn’t work. The metal sheets were too heavy for it, they would bend and fall off at every lifting attempt. So the customer wasted 4,000 EUR instead of saving 56,000.
Thanks for the interview! Is there anything you’d like to add with regard to lifting magnets and magnetic chucks?
I’d like to briefly mention the social impacts of our business. Things like environmental awareness, employee well-being and their wages, the taxes we pay, and so on. Non-European lifting magnets and magnetic chucks are often sold for a price that doesn’t even cover the price of material here. So for those considering the social aspects of their business, getting a European magnet makes total sense.