Robotic arms automatically move steel parts into a machine, then put them back to their place. Zero-point pallet systems eliminate pauses in production and make the most out of a machining tool. Get inspired by real-life examples of how lifting magnets and magnetic chucks help automate our customers' productions.
Automated production cuts down on manual labour, and lifting magnets and magnetic chucks are a popular automation solution. When a workpiece gets lifted or clamped by a magnet, no person needs to be involved.
Many of our customers tackle automated production — either within their own production operations or as part of their business activity based on designing and selling automation solutions for production facilities. Magnets can be used in automated productions in various ways — let’s get inspired by our customers' real operations and solutions.
Magnetic Robotic Arms
Robotic arms are a popular automation solution, and they often come equipped with magnetic clamps or lifting magnets. A robotic arm might lift a steel workpiece from its shelf, place it in a machine, clamp it with the help of a magnetic chuck, and have the machine perform the desired machining operations. When those are done, the robotic arm picks up the workpiece again and returns it to its place.
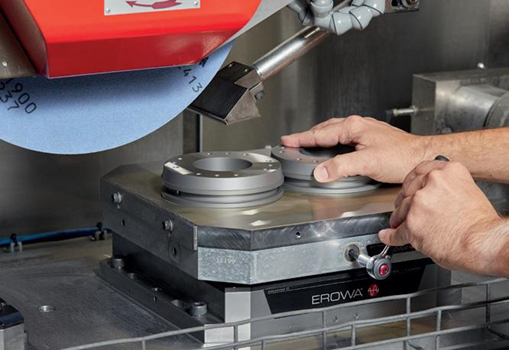
Zero-Point Pallet Systems
In production facilities, time is money. The ultimate goal is to have machines generating value all the time — pauses in production waste resources. You can eliminate these unwanted breaks (almost entirely) when you switch to zero-point pallet systems, forcing machines to produce value almost non-stop.
Our Swiss customer EROWA is a zero-point pallet system specialist. They manufacture modular pallet systems which make it possible to clamp parts for machining outside the machine, on special zero-point metal pallets. These are equipped with magnetic chucks (mostly our Neomicro chucks) onto which parts for machining are arranged.
Pallets with prepared parts are then inserted into the machining tool one after another, with no time spent on adjusting the workpieces while the machine idly stands still.
OUR TIP: Here’s more on how lifting magnets and magnetic chucks save money and speed up a production process. |
Demagnetiser
Production facilities that use magnets to manipulate their workpieces often need to demagnetise the workpieces before they continue in the production chain or before they get shipped away. Demagnetisation is necessary for all the following operations to be safe and efficient — and it can also be automated.
Here's a good example. Our long-term customer Hašpl produces and sells screws and nails. They use our tunnel demagnetiser as an automated step within their production process to demagnetise entire boxes of screws/nails at once. Thousands of screws and nails are demagnetised within a few minutes!
Dormer Pramet in Šumperk, Czechia, uses our tunnel demagnetiser on a stack of steel plates so they don’t attract dust and iron parts. Automated demagnetisation is also effective for getting rid of residual magnetism in steel poles.
Demagnetisation is extremely important in aerospace and automotive production — both these industries have very strict standards when it comes to residual magnetism. When steel dust clings to automotive parts, it complicates further manufacturing operations (e.g., welding and varnishing). In the aerospace industry, residual magnetism can negatively impact the performance of electrical appliances.
OUR TIP: Here’s more on the topic of demagnetisation in production. |
Thinking of getting lifting magnets or magnetic chucks for your production facility? Reach out to us, we’ll be happy to assist you!