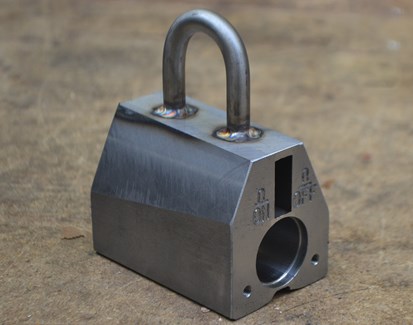
A high-quality lifting magnet has a welded construction, never bolted. The core of a permanent magnet is composed of neodymium. An electromagnet has a heart of coil, an electropermanent magnet has both neodymium and coil inside. Get a sneak peek into our magnetically attractive production!
The “mag” in Walmag stands for magnets, and we often introduce ourselves as a producer of “magnets” — when in fact, our products are lifting magnets and magnetic chucks. The word “magnet” in its true sense should be used only for the actual magnets hidden inside our lifting/clamping devices.
Lifting Magnets Production Step by Step
1. Prepping & Machining
Prep is an essential part of any manufacturing process; for each of our products, the first step is gathering the necessary material and parts. We use only high-quality structural steel for the outer construction of our lifting magnets — we work mostly with European suppliers, and only if we can’t find the exact type of steel we need in Europe do we search in other parts of the world. Yet, we always insist on the steel meeting all European standards.
We machine our steel parts on CNC machines — shaping them first, then welding them together. Welding is a very important moment in our manufacturing process as it’s a sign of quality. Lifting magnets with bolted construction can never match welded magnets — bolts always get loose after some time, which often causes construction deformities resulting in magnets literally falling apart.
OUR TIP: Tell-tale signs of a high-quality lifting magnet. |
2. Inserting Magnets and/or Control Unit
When the outer construction of the lifting magnet is ready, it’s time to insert the actual magnets inside. Magnets differ according to the lifting magnet type — a permanent magnet, electropermanent magnet, or an electromagnet. We insert the parts inside the construction and then set them with epoxide to make sure they stay in place.
Permanent lifting magnets have multiple neodymium magnets inside (the exact number depends on the required lifting capacity of the magnet) as well as a rotor which turns the magnet on & off. When switched on, the magnets rotate so that their magnetic force is directed outside the lifting magnet, attracting ferromagnetic objects in their vicinity. With the switch handle in the OFF position, the neodymium magnets inside rotate in such a way that they only attract each other — their magnetic force is contained inside the magnet.
Lifting electromagnets have a coil inside which gets de/magnetised according to whether the magnet is connected to a power source or not. The coils in Walmag’s magnets are produced by us.
As the next step, we insert a control unit into more advanced electropermanent lifting magnets and lifting electromagnets. Fine electronics get installed and everything is double-checked to make sure it’s 100% functional.
3. Control & Certification
Lifting capacity tests and certification are a crucial (and obligatory) step in our production process. According to legal requirements, every lifting magnet should be able to safely carry three times more than its nominal capacity. This quality is tested during the so-called pull-off test.
At Walmag, we make the pull-off test even more challenging — we insert a piece of paper between the pull-off device and the lifting surface of the magnet, simulating the air gaps that often occur in real life (due to uneven surface of the lifted object — its paint might be peeling off, it could be dusty or otherwise contaminated). Air gaps always make the lifting magnet slightly less powerful, and our demanding pull-off test makes sure our magnets’ lifting capacity is even higher than required by law.
TIP: Více o certifikaci břemenových magnetů se dočtete v článku. Kvalita břemenových magnetů je důležitá i s ohledem na bezpečnost – nekvalitní magnety asijského původu potřebné certifikáty vůbec nemusí mít. |
4. Varnishing, Labelling, Shipping
Once the lifting capacity is confirmed, the magnet gets varnished, labelled and sometimes even accessorised — such as REVOLIFT, our new lifting magnet, which comes equipped with an NFC chip bearing its entire documentation, making it easy to display the magnet’s certification and/or the user manual conveniently on one’s smartphone.
A lifting magnet, properly labelled and packaged, is then sent on its way to our customer.
Making Magnetic Chucks Step by Step
1. Prepping & Machining
The first step in the manufacturing process of magnetic chucks doesn’t really differ from that of lifting magnets. Our magnetic chucks portfolio is quite large, and we use a variety of parts and materials — such as steel sheets for slats of permanent magnetic chucks, and steel & brass for magnetic pole desks. Every magnetic chuck has its detailed production documentation that determines which parts and materials need to be prepped for production.
The prepped parts go to our CNC machines where operators produce the base for a magnetic chuck. Onto the base we assemble the magnetic material — slats on permanent magnetic chucks; magnets on electro- and electropermanent magnetic chucks, closely following the magnet’s production documentation.
2. Magnetic Accessories
If the magnetic chuck has a top pole desk, we machine it and then set magnets on it as well. An assembled magnetic chuck is then subjected to finishing machining operations, gets varnished, and the process is topped off with the final production control to make sure we deliver a perfect product.
Often, magnetic chucks come with a control unit which gets installed at the end of the manufacturing process. A control unit enables the integration of the magnetic chuck and the CNC machine — so that the operator controls both machining and magnetic clamping at once.
Contrary to lifting magnets, magnetic chucks don’t require an obligatory safety check — but that certainly doesn’t mean we don’t test our magnets! We surely do: we measure the magnetic flow inside the magnet and also perform our own pull-off test.
How Long Does the Manufacturing Process Take
The entire manufacturing process takes 4–6 weeks (for both lifting magnets and magnetic chucks). That said, we keep our most popular magnets in stock for quick delivery.
At Walmag, we’re more than just manufacturers — we have our own R&D department, inventing, designing, and producing our own products. We often design customised lifting magnets and magnetic chucks. In these cases, our engineers work closely with the sales department to make sure we meet the customer’s needs and requirements perfectly. For Siemens, for example, we made lifting magnets in unusual shapes and with an adjusted switch handle. We also supply large lifting systems to large production facilities.
Want to find out more about what we offer? Get in touch, we’re always happy to help!