A permanent magnet uses a simple and inexpensive technology. The magnetic force of an electromagnet is unlimited, while an electropermanent magnet is energy-efficient and doesn’t heat up when in use. Read to find out all the differences in the technology of magnetic chucks and lifting magnets, and their pros and cons.
Permanent magnets
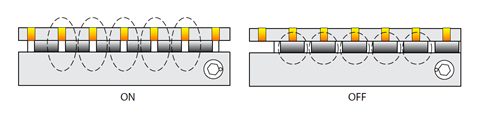
Inside a permanent magnet – its poles in the ON and OFF position
The core of a permanent lifting magnet or a magnetic chuck is made of a ferromagnetic material which creates a magnetic field. Most often, the magnetic core is made of neodymium, iron and boron. Magnets designed for hot environments are made of samarium and cobalt.
A permanent magnet is activated and deactivated by a manual switch lever. With the switch lever in the OFF position, the magnetic field is closed within the magnet. In the ON position, the switch lever moves the magnets inside the magnetic device, changing their polarity as a result. This opens the magnetic field to the outside of the magnet. It closes again when a lifted or clamped object is attached to the magnet.
This technology is quite simple – permanent magnets are therefore relatively inexpensive in comparison to electromagnets or electropermanent magnets and require no electricity for functioning. No electric cable gets in the way during machining or other operations. And they’re easy to install.
But there’s always a flip side of the coin: Permanent magnets need to be switched on manually and the stronger the magnet, the more strength is required to switch it on. This means permanent magnets are limited in magnetic force – it would be impossible to switch really powerful magnets manually.
Our best-seller among permanent magnets is our NEO lifting magnet or its version for hot environment NEO HOT. We describe them in detail in our article on how NEO magnets are used in the Czech branch of Siemens.
Electromagnets
The core of electromagnets is made of a magnetic material (usually cylinder- or rectangle-shaped) with conductive copper coils spooled over the core. When powered by electricity, the coils create a magnetic field; when unplugged, the device is not magnetic at all.
The biggest pro of this technology is the activation and deactivation of the magnet by just pressing a button. This results in an unlimited magnetic force and no residual magnetism (lifted or chucked objects are released immediately after the magnet is turned off).
Electricity also enables regulation of the magnetic force. This makes electromagnets perfect for machining uneven workpieces as they need to be attached by just the right amount of magnetic force (they might get deformed when clamped too tight).
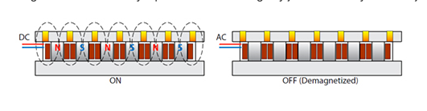
Inside an electromagnet – its poles in the ON and OFF position
The biggest con of electromagnets is obvious – they can’t function without electricity and they need to be plugged in. An electric cable might easily get in the way or get damaged during machining or other operations (e.g., get sprayed by a cooling agent used during milling).
On the other hand, the electric cable is easy to hide during grinding, as the workpiece is usually moved only back and forth. Electromagnetic chucks for grinding are very common. They’re not suitable only for precision grinding (with thousandths of milimetres precision) as they heat up when in operation.
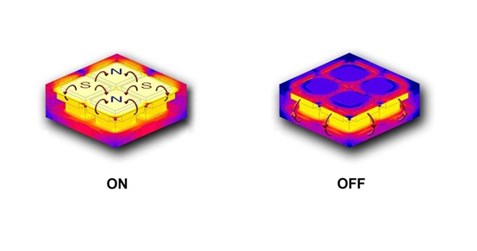
Inside an electropermanent magnet – its poles in the ON and OFF position
Electropermanent magnets
Electropermanent magnets are a cross-breed between permanent and electromagnets. Their core contains permanent magnets activated by a short electric discharge which changes their polarity.
Electropermanent magnets need an electric discharge to become magnetic but once they do, they run independently of electricity.
This makes electropermanent magnets very energy-efficient and practical to use as they don’t need to be plugged in by a cable. Lifting electropermanent magnets have their own battery; electropermanent magnetic chucks do have a cable (which leads to their control unit) but it can be unplugged once the chuck is activated.
There are two types of electropermanent magnets: compensated and non-compensated (compensated magnets are sometimes called double magnetic system magnets).
- The core of a compensated electropermanent magnet is made of permanent magnets of high magnetic force. That goes hand in hand with higher residual magnetism – you have to run a demagnetising cycle before removing a magnetised workpiece from a compensated electropermanent magnet.
- The core of a non-compensated electropermanent magnet is made of magnetic coils only which makes the magnetic device weaker in magnetic force but also means lower residual magnetism. Clamped or lifted workpieces are easily removed.
The biggest pro of electropermanent magnets is that they don’t heat up when in operation. This is extremely important for precision grinding as the hotter the workpiece, the more difficult precision grinding gets.
Our popular electropermanent magnet is the Mastermill Chuck. Read this article to find out more about its properties.
How to choose the best type of a lifting magnet or a magnetic chuck?
Every production is unique and specifics always have to be considered. You have to take into account your machining operations, the weight of your chucked/lifted workpieces, and many other factors.
In Walmag, we always make a customised offer to every customer. Contact us if you want to choose the best type of a magnetic chuck or a lifting magnet.