Workpieces made of magnetic materials are prone to becoming magnetized during machining, drilling, lasering, or other manipulation. That may cause difficulties when doing subsequent work with magnetized workpieces—they attract dirt and may generally become more difficult to machine. Demagnetizing such workpieces eliminates these problems. Handheld, table, or tunnel demagnetizers are commonly used in production; the tool used is determined by the size and volume of the workpieces that need to be demagnetized.
Why do workpieces become magnetized?
Any time you work with products made of magnetic materials, you may unintentionally magnetize them. Most often, unwanted magnetization occurs when metallic workpieces are:
- clamped or lifted using magnetic force,
- welded using magnetic pulse welding,
- bent or straightened,
- punctured,
- induction hardened,
- forged cold,
- drilled or sawed, or
- e.g., marked using a laser.
Cons of a magnetized workpiece
Magnetized workpieces attract metal objects—which creates more friction, in turn decreasing the longevity of the workpiece. In case you need to continue working with a magnetized workpiece, you may face some difficulties, such as:
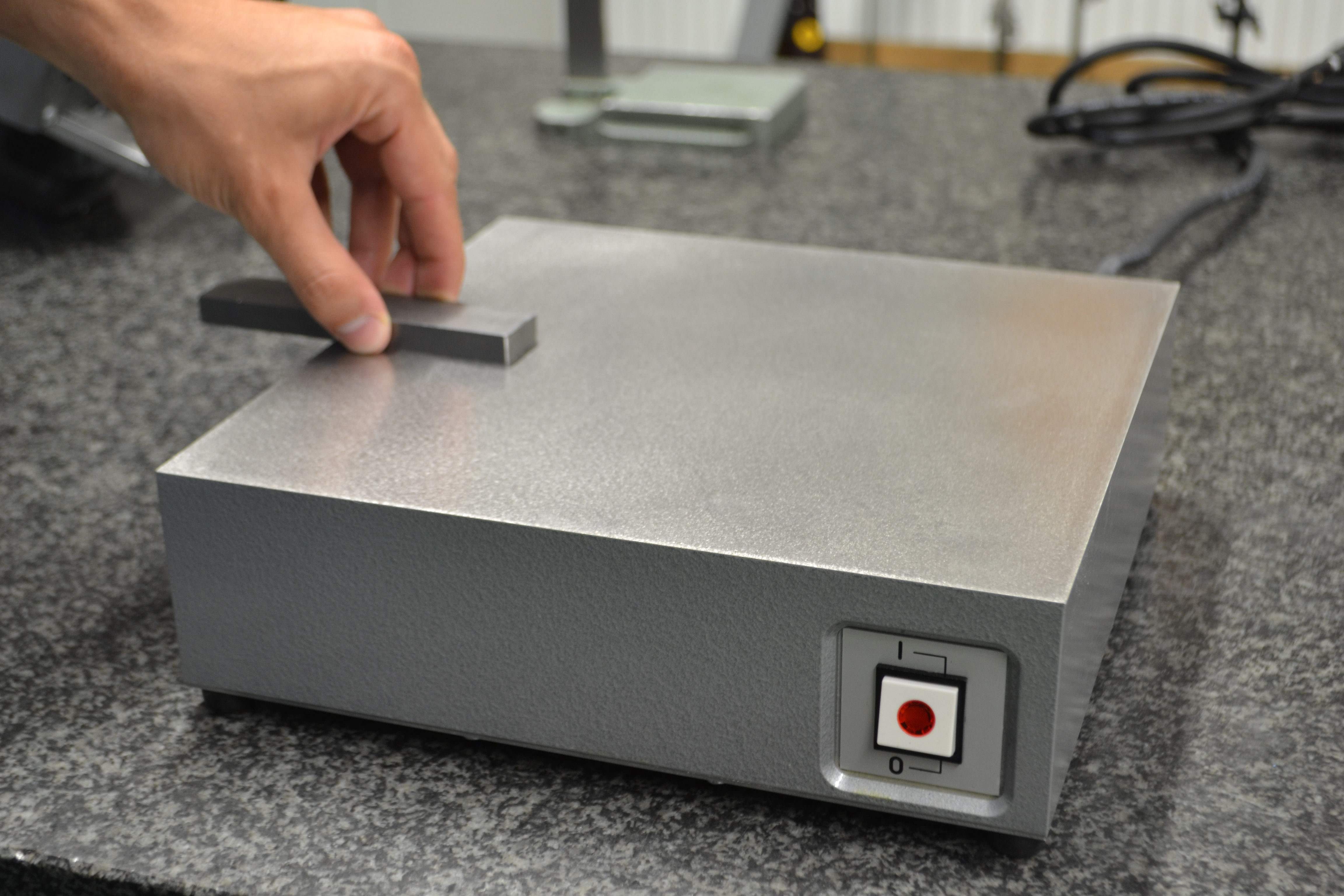
Demagnetization on a table demagnetizer.
- cleaning the workpiece becomes more difficult (workpiece attracts microparticles from the air)
- welding is more complicated or completely impossible,
- galvanisation of metal also becomes more complicated,
- wire cutting becomes very uncomfortable,
- magnetization also causes faults in measuring as magnetization negatively affects the precision of measuring devices.
The degree of magnetization is most often measured in Gauss (Gs) units. Ideally, a workpiece should have less than 5 Gs—at this point it does not attract metal shards and the workpiece is no longer considered magnetized. It is not necessary (as it is almost impossible) for a workpiece to have zero Gs—a low level of magnetization is natural for metallic workpieces. However, if your workpiece is in the double-digit range of Gs, its demagnetization is more than advisable before continuing to work with it.
Demagnetizing workpieces correctly
Workpieces can be easily demagnetized using one of the three types of demagnetizers.
Handheld demagnetizers are the simplest to use—just press the button, place the demagnetizer close to the workpiece, and circle above its entire surface to demagnetize it. In case the workpiece is larger, turn it around and demagnetize it from the other side, making sure it is demagnetized all the way through. Measure the workpiece's degree of magnetization after you finish. If necessary, repeat the process.
Handheld demagnetization is ideal for workpieces with atypical shapes or bulky larger shapes. To prevent scratching the surface, we recommend placing a protective layer between the workpiece and the demagnetizer (like paper or other non-magnetic material, no thicker than 1 mm).
A table demagnetizer is better suited for demagnetizing flat parts or serially produced production parts. Put the table demagnetizer on your work desk or under/above your conveyor. Slide the workpiece from side to side over the demagnetizer’s surface. When demagnetizing strongly magnetized workpieces, you may need to do this repeatedly.
And last but not least, there’s the tunnel demagnetizer—best suited for demagnetizing block-shaped or thin-walled workpieces. Tunnel demagnetizers are often integrated in the workline on a conveyor belt or a roller conveyor.
Slowly slide the magnetized workpiece through the tunnel demagnetizer (no faster than approx. 10 meters per minute), slide it back and measure its residual magnetizm. Repeat the process, if necessary.
Would you like help with demagnetization? Let us know. We would be more than happy to advise you or lend you one of our demagnetizers for a free trial. You can also send us products that you need to demagnetize in your line of work and we will determine the best demagnetizing solution for you.