The most important thing during milling operations is to clamp your workpiece firmly to prevent unwanted movement or vibrations. Mechanical clamps can do just that; however, they always bear a risk of damaging the clamped workpiece. Moreover, mechanical clamps often obscure access to all sides of the clamped workpiece so it has to be re-clamped. Magnetic clamps or chucks can help you avoid these problems.
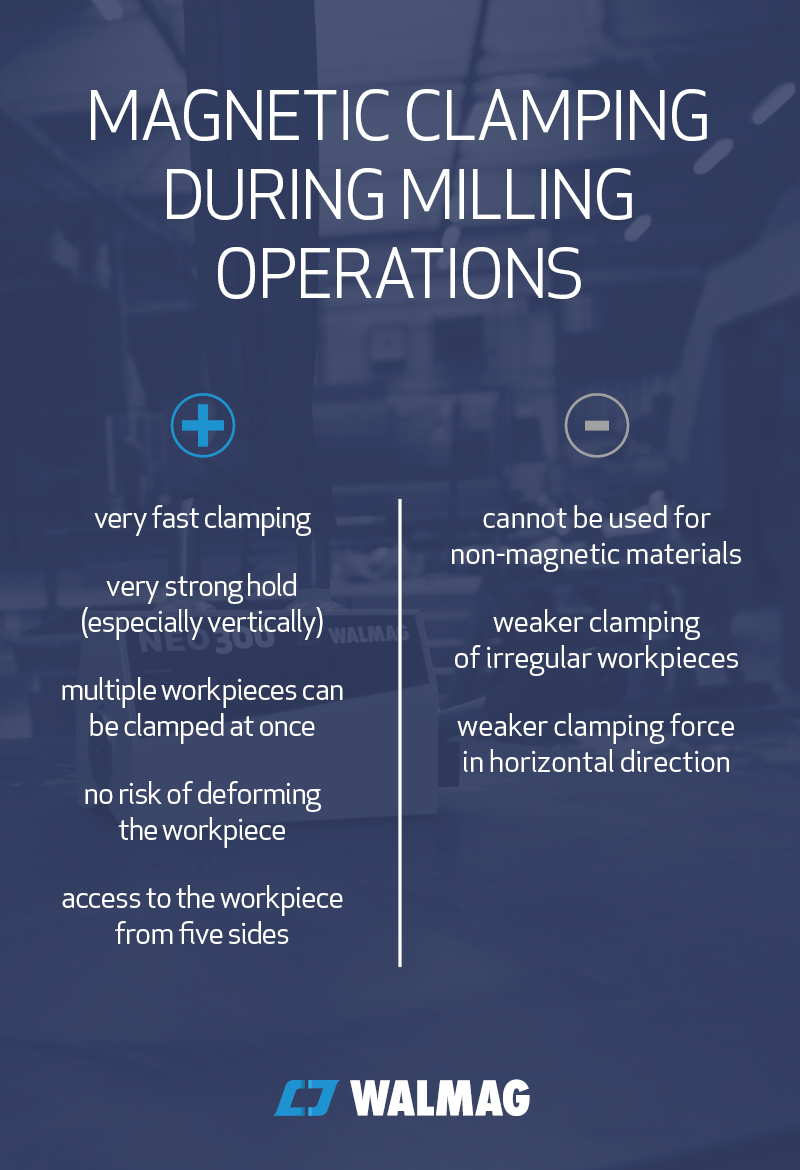
Benefits of milling on a magnet
Compared to mechanical clamps, clamping a workpiece using a magnet is remarkably faster. Workpieces don’t have to be secured in the jaws of a clamp, you simply place them on a workstation with a magnet. That makes the clamping operation much simpler and more efficient, especially when milling multiple smaller workpieces—they can be clamped on a workstation in groups.
There is no risk of deforming the workpiece when using magnetic clamps and chucks. The magnetic force firmly attaches the workpiece to the workstation and fixates it very securely (especially in vertical direction) without any pressure from firm jaws.
Magnetic clamping allows free access to the workpiece from all sides as it has no clamping depth. For example, when milling a cube, you can conduct any desired milling operations from five sides without having to re-clamp the cube. This is possible thanks to pole extensions—flexible or firm cubes or cylinders which can lift the workpiece so that the entire surface of each side can be milled without the mill damaging the clamping magnet.
Pole extensions can copy any bend of a blank workpiece which prevents the workpiece from bouncing back to its original bend once machining is completed. Manual clamps may create tension in the machined workpiece which makes the material bend back after the clamps are loosened.
Benefits of milling on a magnet are maximized when using 4- or 5-axis milling cutters—you can truly use these to their max when combined with magnetic clamping.
Limits of milling on a magnet
Naturally, magnetic clamps cannot be used to secure non-magnetic materials like wood, aluminium, brass or stainless steel. Clamping on a magnet cannot be used for indented workpieces—due to multiple air capsules between the workstation and the workpiece, its fixation can never be sufficient.
In some cases, especially when machining very close to the magnetic surface, magnetic force can complicate discharging and dumping of metal chips (which are magnetically attracted back to the workpiece or tend to attach to the magnetized worktool). This can be easily eliminated by pressure cooling.
Another con of magnetic clamping is its decreasing power in the vectoring of the skid—down to 20%, compared to the vertical direction. To prevent that, we recommend securing the workpiece in the stopper holder or lowering the side pressure during milling work, if possible.
Summary and recommendations
Magnetic clamping of workpieces is ideal for milling operations on flat more robust workpieces made of ferromagnetic materials or for milling multiple smaller workpieces at once. In such cases, the worktool can access the workpiece from five sides, the magnet does not deform the workpiece and the workpiece is clamped quickly, firmly and securely.
On the other hand, we would not recommend magnetic clamping for smaller irregular workpieces—consult an expert beforehand on whether a magnet is suitable for your workpiece.